Why Register?
- List Your Business
- Business Matchmaking
- WhatsApp Chat
- Personal Messaging
- Showcase Your Products
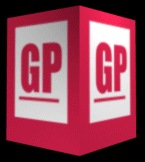
Product Pictures
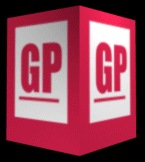
General Plastics, Kenya, one of the largest manufacturer of Plastic products in Kenya has been sourcing Plastics Dryers and Hoppers from Bry-Air since 1995. The company is into the manufacture of plastic packaging by injection moulding, Blow moulding, Using PET, Polypropylene, Polyethylene, PVC, Polystyrene, General Plastics is the largest rigid plastic packaging manufacturer in East Africa and is ISO 9002 certified. We have 5 color printing on plastic containers, unsurpassed in East Africa.
General Plastics is the premier manufacturer of rigid plastic packaging in Kenya and the East Africa region. Our product range includes plastic bottles, jars, tubs, closures, caps and pumps.
Our customers cover the personal care, pharmaceutical, food & beverage, agro-industrial, automotive lubricants,chemical and the household products markets.
In manufacturing we employ blow moulding, injection moulding and stretch blow technologies with a variety of materials including PET, HDPE, Polyproplene, PVC, Polystyrene, LDPE and LLDPE.
Packaging solutions
GP is an integrated packaging solution provider, delivering innovative cutting-edge plastic packaging solutions to its customers.
Be it Preforms, Pet Jars , Bottles, containers, labels, caps/closures, we have an answer to every packaging requirement. When you are first venturing into the complex arena of packaging, it can all be a bit daunting. Are there standard products available or do I need to commission my own design? What material should I choose? What caps/closures are suitable for my product? How can I match the colour to other products in my range? Is it best to print or label? How much will it cost and are there any minimum order quantities? We can manage your project from start to finish.
GP has over 35 years experience and offers inspired design, consistent quality, great customer service and flexibility, and the ability to deliver on time and suit the budget. Whether you choose from our standard products range or require a tailor made exclusive solution, we are always there to help you from the start, and continue every step of the way with product selection, design, support, technical analysis, advice and continued after-sales service.
Call or visit us with your requirements and our experts will work with you to bring your concepts and ideas to a creative life.
Manufacturing
In 1992, GP first introduced injection-moulded "thin-wall" containers used for cooking fats. This new plastic packaging replaced the traditionally used tin containers, and marked a major shift from tin to plastic containers by the manufacturers of edible oils in the region. This was the first injection moulding process available in East Africa and GPL gained many customers who previously relied on tin containers.
In 1996, GP pioneered the use of stretch blow moulding technology in East Africa, using food grade polyethylene terephthalate (PET) as a raw material. This process is used in the manufacture of packaging for food and chemical products such as mineral water bottles, and containers for the pharmaceuticals, juice and cosmetics industries.
In early 1997, GPL bought out Vitaplast Ltd which had been started the previous year as a competitor to GP's packaging manufacturing business. Subsequently Vitapalst Ltd merged with General Plastics Ltd.
GP has continued to initiate innovative plastic packaging solutions for local industries
We have deployed the best of machines, moulds, material and men to ensure that our customers benefit from our technological edge. We collaborate with European and Japanese technology leaders with one single-minded aim to develop innovative and breakthrough packaging solutions that meet the best standards of quality and performance. Ours is just a testimony to the process excellence that we bring to the table. Our 35,000 sq. meters facilities include two state-of-the-art production plants that comply with international food-grade manufacturing standards and a dedicated tool room for all research and development activity